Metal Stamping Technology Conference
Schedule
Monday,
January 27, 2025
Exhibitor Setup
Early-Arrival Downtown Meet and Greet
Ole Red, 300 BroadwayAppetizers and Drinks Provided
Join other attendees, speakers and sponsors at Blake Shelton’s Ole Red for an early arrivals meet and greet. PMA has reserved the mezzanine (2nd floor) where you’ll enjoy great company, delicious appetizers, drinks, and amazing music with Nashville’s hottest talent.
*Thanks to the generous sponsorship of Principal Financial Network, we are able to offer this event at a substantially reduced cost of $45 per person. Be sure to add this to your registration!
Tuesday,
January 28, 2025
Registration/Breakfast/Exhibits Open
Welcome

Keynote: Benchmarking Success: Insights and Trends in the Manufacturing Industry


Laurie Harbour
Partner
Wipfli LLP
View Biography
Keynote: The Manufacturing Renaissance: Driving Continuous Improvement
Manufacturing is in the midst of a marketplace evolution. From new automated and intelligent technology to growing consumer demands, the industry faces many challenges. During her presentation, Laurie will provide a look at the current state of manufacturing and what the future holds for different sectors in 2025 and beyond. She also will share what businesses should be focused on to achieve success and better prepare for the future.
Break
Exploring Real Impacts of Automation and Artificial Intelligence in Metal Fabrication


Will Healy III
Global Industry Segment Leader – Welding
Universal Robots
View Biography
Exploring Real Impacts of Automation and Artificial Intelligence in Metal Fabrication
Metal fabricators from stampers to welders to assemblers are all challenged with workforce woes, the need to boost productivity and the endless quest for quality. Knowing automation is the answer is one thing, but actually finding real success with technology investments can feel challenging and risky. How do you know what will truly bring value to the organization? How do you determine the return? And now with the hype of Artificial Intelligence (AI) seemingly on every product, how do press shop leaders determine the right places to invest limited time and capital?
In this session, we will delve into the ever-evolving landscape of automation and AI in metal stamping and take a look at technologies that are having a real impact today across the shop floor. Then we will stare into the crystal ball to look forward at technologies that are on the near horizon that fabricators should be keeping an eye on. Covering important topics like automated press tending, collaborative automation, data-driven insights, predictive maintenance, robot-guided vision, bin picking, quality inspections, demand forecasting and much more, attendees should leave this session ready to make value-creating technology investments in their business. Join us as we explore how AI is reshaping the press shop—one algorithm at a time.
Lunch/Exhibits Open
Optimizing Production Efficiency: Unlocking Potential with Servo Press Technology


David Diaz, PhD.
Servo Press ScientistNidec Press & Automation
View Biography
Optimizing Production Efficiency: Unlocking Potential with Servo Press Technology
A large number of servo presses in the industry are underutilized. This talk identifies common bottlenecks and explores new strategies to maximize servo press efficiency. Learn practical ways to leverage servo press flexibility and precision, optimizing production and improving overall performance. Whether aiming to increase throughput, reduce setup times or enhance product quality, this presentation offers actionable insights tailored to boost manufacturing capabilities.
Break
Optimizing Servo Press Technology to Deep Draw 17-7 PH Stainless Steel
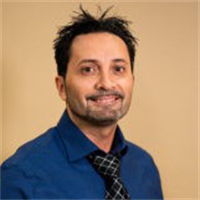
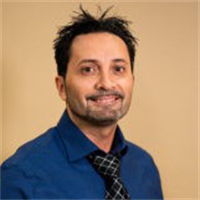
Manny Resendes
Engineering/Toolroom ManagerLarson Tool & Stamping Company
View Biography
Optimizing Servo Press Technology to Deep Draw 17-7 PH Stainless Steel
This presentation is a case study that explores the advantages of utilizing servo press technology for deep drawing components from 17-7 PH stainless steel. Attendees will gain real-world insight into the precise control and programmable motion profiles offered by servo presses, which enhance process flexibility, reduce quality burden and improve overall run quality at high volumes.
Break
Servo Press and In-Die Transfer Technology


Bob Gunst
PresidentJacar Systems LLC
View Biography
Servo Press and In-Die Transfer Technology
Servo presses and in-die transfer are new and exciting technologies that are emerging in the sheet metal-stamping industry. In this session attendees will learn how to combine these two technologies to maximize project outcomes. Participants also will see examples of different servo applications using in-die transfer tools, learn valuable press stroke and transfer motion tips and tricks, and take away several case study illustrations.
Networking Reception/Exhibits Open
Wednesday,
January 29, 2025
Registration/Breakfast/Exhibits Open
Day Two Welcome

Keynote: GE Appliances New Zero-Distance Formability/Feasibility Process
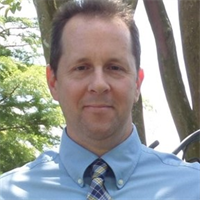
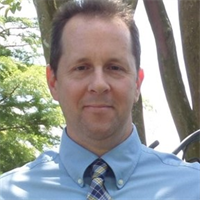
John Panozzo
Senior Advanced Engineer
GE Appliances & Lighting
View Biography
Keynote: GE Appliances New Zero-Distance Formability/Feasibility Process
GE Appliances (GEA), a Haier company, has undergone sweeping internal transformation since 2016, driven by a “zero distance” strategy: zero distance between what the company makes and what its customers want; between ideas and innovation; and between where products are developed and made. Toward that end, GEA has transformed its business model toward a seamless and digital supply chain—internally and externally.
Break
The Evolution of Press Operator to Stamping Technician


Peter Ulintz
PMA Technical Consultant
Pace Technologies, LLC
View Biography
The Evolution of Press Operator to Stamping Technician
Historically, press operators have been considered lower-skilled entry-level positions with little (or limited) decision-making ability in most stamping plants. Today, press shop personnel are responsible for setting and operating press lines costing hundreds of thousands or multi-million dollars that contain dies that can cost more than most houses. In addition, they are increasingly responsible for improving productivity, maintaining product quality, minimizing downtime, and protecting the integrity of the dies and press. This presentation explores the need to transform the traditional press operator to a highly skilled apprenticed technician who views the metal stamping process as “math in motion.”
Lunch/Exhibits Open
Speaker and Topic TBA
Break
Secret S.A.U.C.E. to Stamping Optimization
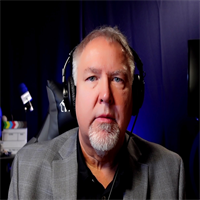
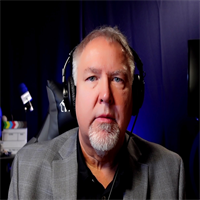
Dean Phillips
Director of Technical Training
Precision Metalforming Association
View Biography
Secret S.A.U.C.E. to Stamping Optimization
In this presentation, you’ll gain concrete executable ideas to improve your production in your press shop using Dean Phillips’ S.A.U.C.E method. Minding the categories of Safety, Automation, Utilization, Comparison and Education will deliver instant results in any plant, regardless of size or stamping operation. These tangible, proven concepts will bring your team ideas on how to fully optimize your facility’s operation. This presentation is valuable to leaders, die setters, tool and die personnel, operators and engineers.
Closing Remarks
